On January 29th, an international team led by Yihui Zhang, Associate professor from the School of Aerospace Engineering at Tsinghua University, John A. Rogers, Louis Simpson and Kimberly Querrey Professor at Northwestern University, and Yonggang Huang, Walter P. Murphy Professor at Northwestern University, published their collaborative work as an article in Nature Materials. This research paper, entitled “Morphable 3D mesostructures and microelectronic devices by multistable buckling mechanics”, reported a novel route that relied on elastomer platforms deformed in different time sequences to reversibly alter the 3D geometries of supported mesostructures via nonlinear mechanical buckling. Using this new approach, an adaptive radiofrequency circuit, a concealable electromagnetic device, and other functionally reconfigurable microelectronic devices were designed and demonstrated.
Reconfigurable 3D structures have widespread applications in diverse sectors of areas such as biomedical devices, microelectromechanical systems (MEMS), robotics and metamaterials. The existing fabrication approaches are, however, constrained by the compatible range of materials and length scales. Specifically, they are not readily applicable to micro/nanoscale architectures, or to high-performance, planar thin film materials. These limitations set practical constraints to the further development of reconfigurable 3D microelectronic devices.
Prof. Yihui Zhang’s group collaborated closely with the groups of Prof. John A. Rogers and Prof. Yonggang Huang in the development of a new approach for reconfigurable 3D mesostructures based on multistable buckling mechanics. This approach leverages controlled compressive forces to deform 2D patterned film precursors into desired 3D structures. By changing the sequences (or loading paths) of compressive deformations, the supported 3D structures can be altered reversibly between different shapes. This strategy is applicable not only to diverse feature sizes, but also to a broad set of materials (e.g., conductors, semiconductors and insulators), due to the compatibility with the planar microelectronic technologies available in semiconductor industries. This Nature Materials paper elucidated the design concepts of multistable buckling and the underlying mechanics of 3D reconfiguration, and established general rationales for designing the 3D mesostructures. Experimental demonstrations of more than 20 examples illustrate the versatility of the approaches. Concealable RF antennas enabled by this approach represent an application in reconfigurable 3D RF electronics. The device that spanned a wide range of frequencies (from ~ 6 GHz to ~ 30 GHz) could be switched reversibly between the working mode and concealing mode. Here, the concealing mode was achieved through an electromagnetic shielding that led to dramatically reduced radiant efficiencies, such that it is hard to detect the device.
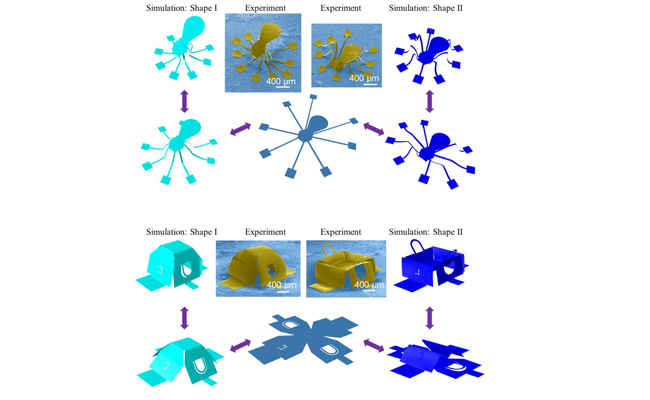
Figure 1. Process of the 3D reconfiguration for two representative morphable mesostructures. The top frame shows the reversible switch between a ‘micro-octopus’ and a ‘micro-spider’, and the bottom frame shows the reversible switch between a ‘micro-house’ and a ‘micro-basket’. The patterned 2D films are assembled into Shape I after simultaneous biaxial compression and Shape II after sequential compression along two perpendicular directions.
Prof. Yihui Zhang, Prof. John A. Rogers and Prof. Yonggang Huang are co-corresponding authors of this paper. Haoran Fu, a postdoc from the School of Aerospace Engineering at Tsinghua University, and Kewang Nan, a Ph.D. student at the University of Illinois at Urbana-Champaign, are the co-first authors of this paper. These studies received support from the National Natural Science Foundation of China, the Thousand Young Talents Program of China, the National Basic Research Program of China, etc.
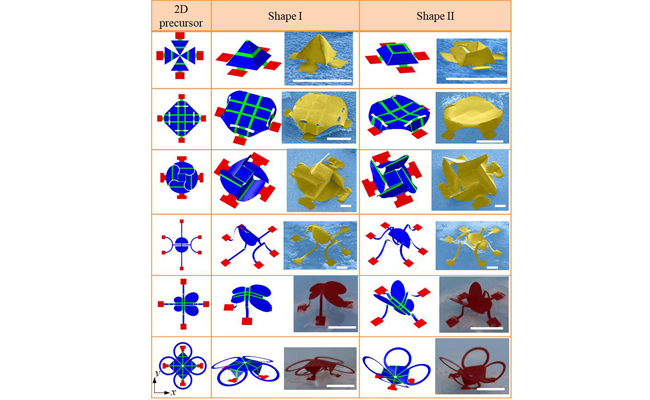
Figure 2. Experimental and computational results on six representative examples of reconfigurable 3D mesostructures. Scar bars, 400 μm for first four examples and 4 mm for the last two examples.
Links to the publication:
https://www.nature.com/articles/s41563-017-0011-3
Editor: Lvhe Zhu